These stories were provided by five of CIM's Industry Partners and originally appeared in the December 2023 - January 2024 issue of CIM Magazine (view it in flip format here).
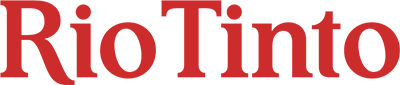
Driving change towards zero-emission trucks and mobile equipment
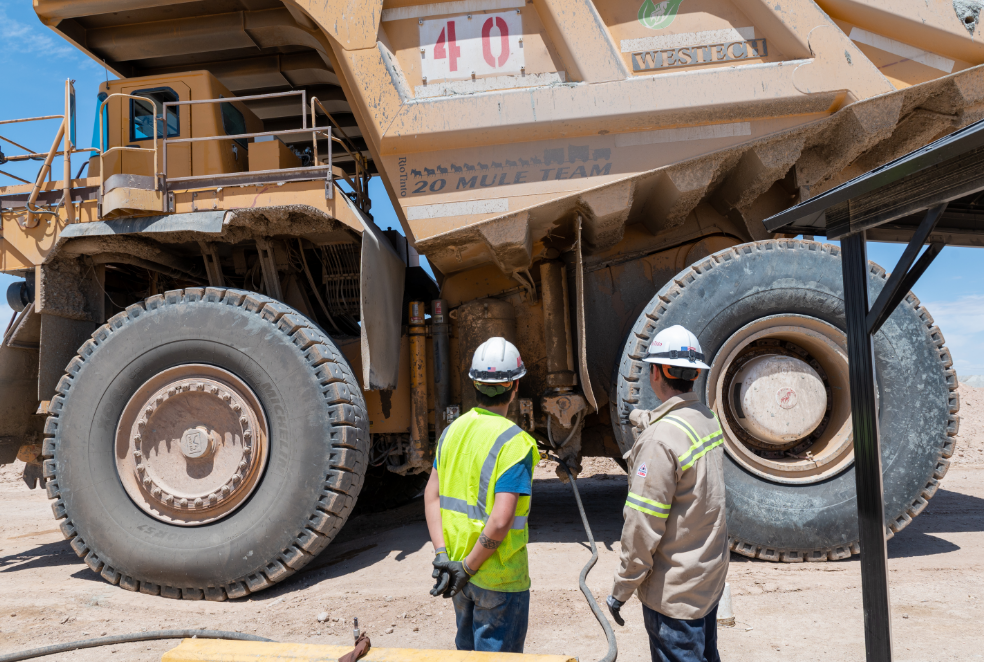
Fuelling up a truck with renewable diesel at Boron, California
In June 2023, Rio Tinto announced it had fully transitioned the heavy machinery at its Boron operation in California from fossil diesel to renewable diesel—making it the first open-pit mine in the world to achieve this milestone. The conversion to renewable diesel brings with it an anticipated CO2 equivalent reduction of up to 45,000 tonnes per year, comparable to eliminating the annual emissions of approximately 9,600 cars.
An initial trial of switching fossil diesel to renewable diesel in a haul truck at Rio Tinto’s Borax mine in California was conducted in partnership with Neste and Rolls-Royce in 2022. It used Neste MY Renewable Diesel, a hydrotreated vegetable oil (HVO) made from sustainably sourced, renewable raw materials, such as used cooking oil and animal fat from food industry waste. Results showed that a truck running on renewable diesel delivered similar performance and reliability as trucks running on conventional diesel.
When used in its purest form, Neste MY Renewable Diesel can deliver up to 75 per cent less greenhouse gas emissions over the full life cycle of the fuel than conventional diesel.
Based on these positive results, Rio Tinto U.S. Borax continued to work with Rolls-Royce, Neste, the United States Environmental Protection Agency and the State of California to fully transition its heavy machinery fleet onsite to renewable diesel at the end of May 2023. This transition included all the heavy machinery on the property from haul trucks to loaders. Renewable diesel is even used in blasting. This conversion to renewable diesel supports Rio Tinto’s global decarbonization objectives, which include a 50 per cent reduction in Scope 1 and 2 emissions by 2030, and a commitment to reach net zero by 2050. Carbon emissions from the use of diesel in its mobile fleet and rail accounted for 13 per cent of Rio Tinto’s Scope 1 and 2 emissions in 2022.
Read more: Hecla | B2Gold | MineSense Technologies | Teck
Given the success at Boron, Rio Tinto conducted a trial at its Kennecott copper operation in Utah.
The company partnered with Cummins, which manufactures engines and related technologies, to trial renewable diesel at Rio Tinto’s Kennecott site in Bingham Canyon in Utah, and results confirmed it is reliable as an alternative fuel.
Over the seven-month trial, the team tested acceleration, speed, cycle times, fuel usage and engine inspection reports for two trucks running on renewable diesel versus two trucks running on conventional diesel, using the same methodology as the Boron team to compare the results.
Diesel accounts for the largest portion of Kennecott’s greenhouse gas emissions, and renewable diesel could provide one component in the overall mix of solutions that will be needed for decarbonization.
An electric future
A battery electric vehicle operating at Kennecott’s underground operations in Utah.
While the biodiesel is a drop-in solution, supply at scale is still a challenge. Achieving decarbonization targets requires other solutions for the long term, including battery electric mobile equipment and renewable energy generation and storage.
Rio Tinto is working on projects to progress the electrification of its mobile fleet at its Pilbara operations in Australia—including haul trucks, mobile equipment and rail operations.
To support repowering its mobile fleet, the company is also working to transition its iron ore operations away from gas-powered generation to renewable solar and wind power. The company is working on delivering the first one gigawatt of renewable energy, which will abate about a third of its 2021 total Scope 1 and 2 emissions across its iron ore business.
At Rio Tinto’s Kennecott mine, the company is also trialing a Sandvik battery electric haul truck and loader as part of underground development work to improve health and safety, increase productivity and reduce carbon emissions.
Across the mining industry, there has been a long-held view that bigger is better. Enormous haul trucks provide economies of scale, allowing operations to move more material, more quickly, by leveraging the large trucks’ power and carrying capacity.
Rio Tinto is challenging thinking on size. Larger haul trucks, while already automated, consume more energy than current electric vehicle (EV) power sources can generate. By exploring truck size, Rio Tinto wants to assess how big and small trucks can both be a part of the solution to reduce emissions in the Pilbara region, where it has several iron ore assets, and find fit-for-purpose solutions in mining.
At its Channar mine in the East Pilbara, the company is working with Scania, a Swedish manufacturer of commercial vehicles, to trial more agile automated trucks that could be electrified more readily to reduce carbon emissions, which could improve their speed to market.
The two companies have established a long-term research-and-development collaboration agreement for the continuous advancement of this autonomous technology, under which Rio Tinto’s Channar mine has become the first active partner site for Scania’s autonomous mining solution. The partnership also includes options for the future transition to electric-powered vehicles.
Rio Tinto is also exploring options to further reduce emissions of larger trucks through its partnerships with Komatsu and Caterpillar. The company is working with both partners to develop its future 220t+ zero emissions autonomous haul trucks, including key development programs and milestones for early operational deployment.